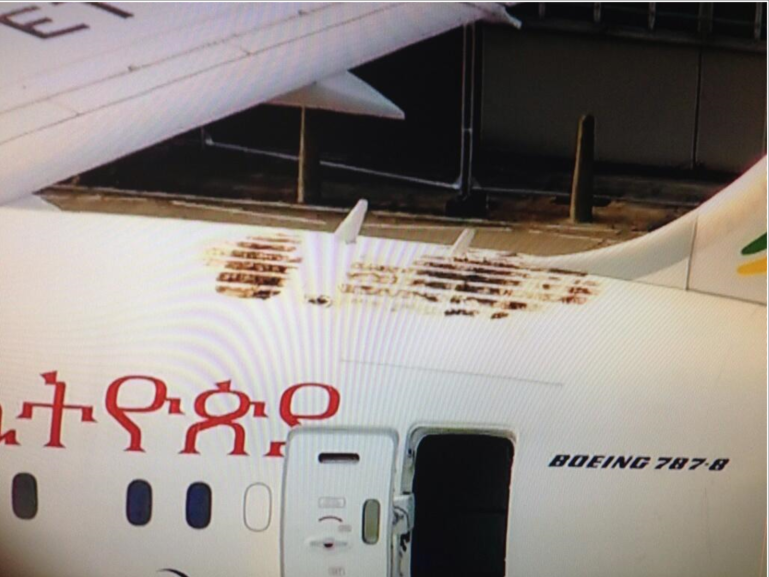
Rynek dużych samolotów pasażerskich o konstrukcji kompozytowej, rośnie z roku na rok o około 186 sztuk (Za rok 2016 dostarczonych: B787 – 137szt., A350 – 49szt.). Nowoczesne technologie i materiały zastosowane w tak dużych konstrukcjach wymagają ogromnej wiedzy, doświadczenia i uwagi podczas codziennej eksploatacji jak i obsługi rutynowych przeglądów. Mechanicy, którzy otrzymali licencję na obsługę B787/A350, są przygotowywani i szkoleni kilka miesięcy u producentów w centrach szkoleniowych. Wymagania stawiane mechanikom to podstawowa wiedza teoretyczna o konstrukcji samolotu i materiałach w niej zastosowanych. W grupie tej znajdują się inżynierowie strukturalni oraz mechanicy technologowie potrafiący odbudować uszkodzoną konstrukcję kompozytową.
Do dzisiaj na całym świecie zdarzyło się kilka drobnych incydentów, gdzie konstrukcja kompozytowa uległa uszkodzeniu. Jednym z pierwszych groźnych przypadków był pożar instalacji ELT (emergancy locator transmitter) na pokładzie B787 linii Ethiopian na lotnisku Heathrow pod Londynem w 2014r. Pożar spowodował poważne uszkodzenie fragmentu górnej sekcji (korony) kadłuba w tylnej części samolotu. Egzemplarz był nowy, w związku z czym operator, właściciel i ubezpieczyciel szybko podjęli decyzje o jego naprawie a nie wycofaniu z eksploatacji. Producent po analizie uszkodzenia podjął decyzję, że jedynym sposobem odbudowania konstrukcji jest wstawienie nowego fragmentu kadłuba. Z linii produkcyjnej zdjęto gotową do montażu na innym samolocie, sekcję kadłuba. Z tej części wycięto taki fragment konstrukcji, która miała odbudować właściwości konstrukcji. To spowodowało opóźnienie na całej linii produkcyjnej modelu B787. Producent w swoich analizach statystycznych przy opracowywaniu standardowych napraw konstrukcyjnych, nie brał pod uwagę, że ten fragment samolotu może zostać uszkodzony w taki lub inny sposób. A w związku z tym, nie zakładał przygotowania jakiegokolwiek rozwiązania w postaci naprawy kompozytowej na taka skalę. Typowe uszkodzenia kadłuba jakie maja miejsce, znajdują się w dolnych częściach samolotu, tam gdzie operuje obsługa naziemna, catering, inne służby wspomagające oraz nie przewidywalne czynniki. Czynnik ludzi ma największy udział w zdarzeniach związanych z obsługą płatowca.
Największym wyzwaniem w technologii konstrukcji kompozytowych jest odtworzenie ich własności wytrzymałościowych tak aby osiągnąć jak najbardziej zbliżone wymagania projektowe konstrukcji. Skomplikowany stopień budowy powoduje, że proces zaprojektowania i wykonania naprawy jest czasochłonny i na najwyższym stopniu skomplikowania. Wynika to przede wszystkim z właściwości włókiem kompozytowych i technologii jakie należy użyć. W konstrukcjach metalowych stosuje się najbardziej podstawowe techniki odbudowy struktury poprzez proces nitowania ( w większej ilości przypadków) i klejenia (szczątkowe). Dzisiaj można powiedzieć, że naprawy konstrukcji metalowych są opanowane prawie ze 100% pewnością i do przewidzenia. Dane statystyczne zbierane przez producentów i nadzory lotnicze potwierdzają, że zaprojektowane i modyfikowane naprawy blacharskie są bezpieczne i niezawodne. W większości przypadków zachowania konstrukcji metalowych zostały rozpoznane.
Jeśli chodzi o struktury kompozytowe, wykorzystanie na tak wielką skalę jaka jest w dużym lotnictwie sprawia, że z każdym nowym przypadkiem będzie możliwość odkrycia i analizy nowych zachowań materiału. Tutaj trzeba wziąć pod uwagę czynnik w postaci odbudowanej/naprawionej konstrukcji kompozytowej tj. naprawy. To z kolei można podzielić na kolejne czynniki, od jakości i dokładności wykonania naprawy, do stopnia skomplikowania struktury elementu i umiejętności mechanika. I w tym miejscu zaczyna wkraczać nowa technologia w postaci robotów, która ma wykluczyć błąd ludzki. Na dzień dzisiejszy wszystkie naprawy kompozytowe robione są ludzką ręką. Jak wiemy, człowiek nie jest doskonały ale się stara. Nie mniej, nie ma powtarzalności wykonania napraw. Obecnie jest kilka firm na świecie, gdzie opracowują systemy robotów do napraw kompozytowych.
Proces naprawy można podzielić na kilka etapów. Pierwszy z nich to określenie położenia uszkodzenia na konstrukcji. Wiąże się to po pierwsze ze zidentyfikowaniem budowy konstrukcji, tj. z jakich elementów jest zbudowany (poszycie, wręga, podłużnica) i z jakich materiałów (metal, kompozyt). Położenie uszkodzenia należy znaleźć według charakterystycznych punktów takich jak wręga, podłużnica, krawędź elementu lub otworu, linia (szew) nitów. Mechanik posłuży się standardowo dostępnymi narzędziami takimi jak linijka, suwmiarka, głębokościomierz. Jeśli porównamy wyniki wykonanych pomiarów przez kilku mechaników, dane nie pokryją się w 100%. Wynika to z indywidualnej oceny jak i również dokładności jaką przyjmie do mierzenia każdy człowiek. Po określeniu pozycji, należy zwymiarować uszkodzenie tj. podać długość, szerokość, głębokość na jakiej jest (np. rozklejenie, rozwarstwienie). Aby poprawić powtarzalność pomiarów trzeba wprowadzić urządzenia/roboty. Już dzisiaj są opracowane urządzenia skanujące, wymiarujące i wykrywające brak ciągłości w strukturze kompozytowej (np. dentCHECK 8tree.com do pomiaru deformacji zewnętrznych). Zebrane dane należy porównać z dokumentacją techniczną samolotu, która precyzyjnie określa co należy zrobić w danym przypadku. Producent dopuszcza do lotu pewną grupę uszkodzeń, które nie stanowią zagrożenia dla konstrukcji podczas dalszej eksploatacji. Jeśli jednak uszkodzenia nie kwalifikują się do tej grupy, tzn konstrukcja nie jest na tyle sztywna aby przenosić obciążenia, należy wykonać naprawę konstrukcji. Dokumentacja kieruje nas do odpowiedniego rozdziału, w którym są zawarte podstawowe instrukcje napraw. Jednak zdarzają się uszkodzenia, kiedy to należy skontaktować się z producentem sprzętu lub organizacją posiadająca odpowiednie certyfikaty (PART-21).
Naprawa. Jest to kolejny etap, który wprowadza nas do tajników wiedzy o samolotach. Jest to w wielu przypadkach czasochłonny proces technologiczny a co za tym idzie bardzo kosztowny. Wynika to przede wszystkim z czasu oraz ceny jednostkowej roboczogodziny wykwalifikowanego personelu lotniczego. Zakłada się, że opłacalność napraw jest do około 60% wartości elementu naprawianego. Powyżej tej wielkości, części są wymieniane na nowe lub samolot może iść do kasacji.
Proces naprawy rozpoczyna się od usunięcia uszkodzonych fragmentów struktury. Następnie – w większości przypadków – należy przygotować powierzchnię zdrowego kompozytu do naklejenia warstw naprawczych. Jest to proces ukosowania lub schodkowania kolejnych warstw. Jest to najtrudniejszy etap w całym procesie wykonania naprawy kompozytowej. Tutaj jest potrzeba posiadania ogromnej cierpliwości, dokładności w ręku oraz wzroku. Odbudowane warstwy muszą być maksymalnie zbliżone do założeń konstrukcyjnych projektowych. Jak wcześniej zostało to wspomniane, powtarzalność człowieka jest bardzo trudnym czynnikiem do osiągnięcia w tym przypadku. Krytyczne wymagania producentów samolotów przy wykonywaniu napraw, zmusiły wiele firm i instytucji badawczych do zaprojektowania urządzeń robotów do precyzyjnego usuwania poszczególnych warstw kompozytowych z dużą dokładnością. Wyzwaniem jest możliwość usuwania poszczególnych warstw bezpośrednio na płatowcu. Pierwszą metodą jaką udało się zastosować w zdalnym urządzeniu to frezowanie poszczególnych warstw. Pionierem w tym jest niemiecka firma DMG MORI/SAUER (www.compositesworld.com/articles/aircraft-composites-repair-moves-toward-maturity). Jednak z uwagi na gabaryty urządzenia i jego masę, urządzenie nie zostało jeszcze zatwierdzone przez producentów. Kolejną metodą która jest w tej chwili badana to usuwanie warstw za pomocą wiązki lasera. Urządzenie jest mniejszych rozmiarów. (https://www.compositesworld.com/articles/primary-structure-repair-the-quest-for-quality). W opracowaniu jest również „nowa” znana od dawna metoda piaskowania. Na ostatnich targach branżowych MRO w Londynie, francuska firma przedstawiła robota, który metodą piaskowania usuwał poszczególne warstwy. Z pośród tych trzech metod, największe nadzieje daje metoda piaskowania.
Po przygotowaniu obszaru naprawy, usunieciu uszkodzonych warstw i luźnych fragmentów konstrukcji, mechanik przygotowuje odpowiednio przycięte warstwy materiałów kompozytowych (węglowe lub szklane w zależności od wymagań producenta). Rodzaj materiału nośnego oraz osnowy narzuca producent. W zależności od stopnia ważności konstrukcji, można stosować łaty robione na mokro (wet lay-up) przygotowywane na miejscy przez mechanika lub prepregi (materiał przygotowany do szybkiego użycia. Na tym etapie jedną z najważniejszych rzeczy na jakie należy zwrócić uwagę to układanie poszczególnych warstw w odpowiednim kierunku. Niejednokrotnie instrukcje naprawcze narzucają dodanie dodatkowej jednej lub więcej warstw naprawczych. Jest to warunek zwiększający współczynnik bezpieczeństwa odbudowanej struktury nośnej elementu.
Ostatnim etapem równie ważnym jak pozostałe, jest utwardzenie kompozytu. Dokładność wykonania worka próżniowego (Vacuum Bag) ma ogromny wpływ na poprawnie wykonaną naprawę. Przy wielu procesach technologicznych przez jakie przechodzi naprawa kompozytowa, łatwo jest o pomyłkę. Wystarczy jedna nie odklejona warstwa rozdzielcza (folia) od prepregu, lub nie wystarczający proces grzewczy, nie odtłuszczona powierzchnia klejenia i cały proces należy rozpocząć od nowa. Jesteśmy na etapie, gdzie małymi krokami pewne czynności naprawcze wykonywane do tej pory przez człowieka, zostaną zastąpione robotami. Konstrukcje stają się coraz bardziej skomplikowane, a technologie naprawcze coraz bardziej wymagające. Ale nic nie odbierze człowiekowi wyobraźni, myślenia i nadzorowania procesów naprawczych, które za każdym razem są inne.
Prezentacja live: tutaj