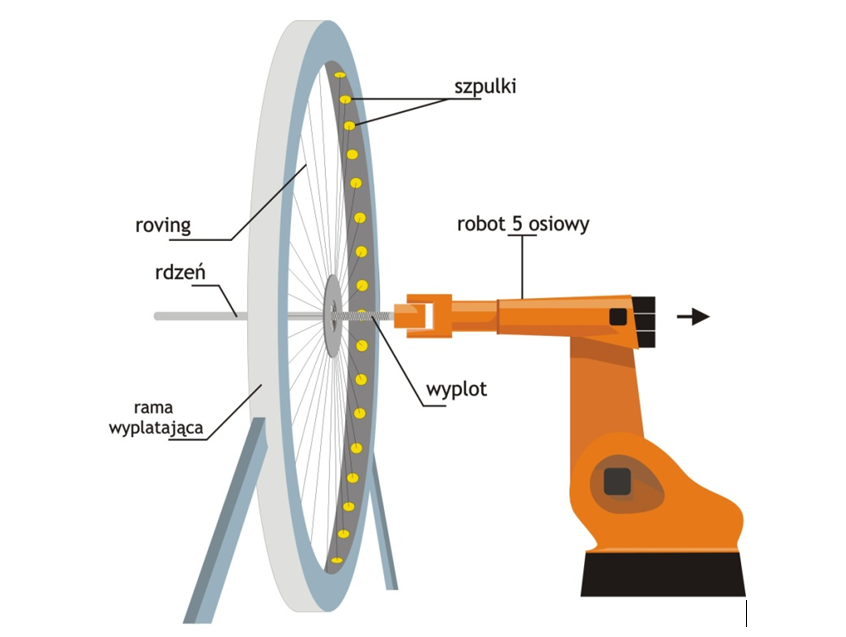
Metoda wyplatania jest prostym, a zarazem bardzo efektywnym procesem służącym do wytwarzania zamkniętych profili półfabrykatów bądź gotowych produktów z włókien ciągłych. Sam proces wywodzi się bezpośrednio od metody oplatania liny bądź warkocza, który zmechanizowano stosując 3 obracające się szpulki, poruszające się po zarysie „8”.
Rys. 1. Automatyzacja procesu splatania liny a) Schemat procesu poruszania się lalek pomiędzy tarczami b)
Odpowiednio zwiększając liczbę lalek w tym układzie oraz zmieniając trajektorię ich ruchu możliwe jest uzyskanie materiału w kształcie taśmy bądź rękawa. Lalki bądź szpulki poruszają się pomiędzy tarczami, które połączone są z kołami zębatymi za pomocą wałów. Tarcze te posiadają zazwyczaj 3 badz 4 gniazda pozwalające na przemieszczenie się lalek w dwóch kierunkach (Rys. 1a). Pomiędzy tarczą nośną a kołami zębatymi znajduje się płyta z prowadnicami w postaci rowków, które pozwalają na pełną synchronizację ruchu szpulek (Rys. 1b.).
W zależności czy droga pokonywana przez szpulki posiada jeden obieg zamknięty czy dwa obiegi zamknięte możliwe jest wykonanie taśm płaskich bądź profili zamkniętych takich jak węże. W przypadku jednego obiegu zamkniętego szpulki poruszają się zgodnie z ruchem wskazówek zegara, natomiast w dwóch obiegach, szpulki drugiego obiegu poruszają się w przeciwnym kierunku. Istnieją również konstrukcje wyplatarek pozwalające na wyplot preform o przekroju „I”, dzięki zastosowaniu połączonych dwóch obiegów zamkniętych. Często wały oraz szpulki posiadają otwory umożliwiające zastosowanie włókien dodatkowych. Podczas wytwarzania preform ciągłych niezbędne jest zastosowanie urządzeń odciągających materiał wyplatany, a prędkość tego procesu wraz z szybkością poruszania się szpulek oraz średnicą rdzenia determinuje kąt ułożenia włókien w wyplocie.
Warto zaznaczyć, że występują wyplatarki o szpulkach umieszczonych równolegle bądź prostopadle do rdzenia, na którym wyplatany jest materiał wzmocnienia. W przypadku pierwszych średnica tarczy prowadzącej ma wpływa na kąt wyplotu, natomiast w drugich średnica nie wpływa bezpośrednio na kąt wyplotu.
Stosując wyplatarki o dużej średnicy wraz z rdzeniem zamocowanym do robota bądź manipulatora zwiększa się w znaczny sposób funkcjonalność maszyny. Duża sztywność ramienia robota pozwala na zamocowanie rdzenia o dużej masie zapewniając zarazem precyzyjny ruch oraz synchronizację z ramą wyplatającą. W konsekwencji gwarantuje to dużą szybkość oplatania wraz z powtarzalnością całego procesu.
Główną zaletą procesu wyplatania w porównaniu do produktów wzmocnionych jednokierunkowo bądź laminowanych jest zdolność dostosowania wyplotu do nietypowych kształtów rdzeni oraz zachowanie ciągłości włókien podczas zmiany średnicy rdzenia. To pozwala na wykonanie owalnych, prostokątnych jak również innych stało-przekrojowych kształtów, czego przykładem mogą być rury, kanały wentylacyjne, wędki. Wyplatanie trójosiowe pozwala wykonywać elementy o przekrojach niejednorodnych, gdzie proces przebiega równocześnie w trzech płaszczyznach [6].
Jak zostało już wspomniane, wyplatanie to szybki i zautomatyzowany proces, w którym koszty związane z układaniem włókien są minimalne, a preformy wytwarzane są znacznie dokładniej i szybciej w porównaniu z konkurencyjnym procesem nawijania. Odkąd praca ręczna obejmuje od 60 do 80 % kosztów całkowitych większości wytwarzanych elementów kompozytowych, jej redukcja dzięki zastosowaniu metody wyplatania pozwala obniżyć w znaczny sposób cenę gotowego wyrobu. [7]
Kolejną zaletą tej metody jest wykorzystanie włókien suchych, dzięki którym zbędne jest użycie „prepregów” podwajających cenę produkcji. Niskie koszty robocizny, jak również stosowanych materiałów predestynują tę metodę do wykonywania elementów kompozytowych wzmocnionych włóknami ciągłymi szczególnie w przypadku profili zamkniętych o przekroju kołowym, takich jak rury i kształtki. Dodatkowo istnieje możliwość zintegrowania systemów monitoringu, takich jak światłowodowe siatki Braga czy różnego rodzaju sensory, pozwalające na kontrolę działania struktur w trakcie całego ich życia. Materiały wyplatane mogą być również łączone z innymi tkaninami wzmacniającymi poprzez zszycie lub sprasowanie bezpośrednio przed procesem infiltracji.
W procesie wyplatania elementów o nieskomplikowanym kształcie wykorzystywane są maszyny wyplatające składające się z obrotowego wrzeciennika, na którym przemieszczają się wokół siebie szpulki z nawiniętymi włóknami ciągłymi (Rys. 2a). Kąt ułożenia włókien zależny jest od średnicy i szybkości posuwu rdzenia. Istnieje możliwość pełnego kontrolowania tej szybkości dzięki sterowaniu komputerowemu, który współpracuje z maszyną wyplatającą. Przykład takiej maszyny oraz schemat zostały przedstawione na rysunku 2b.
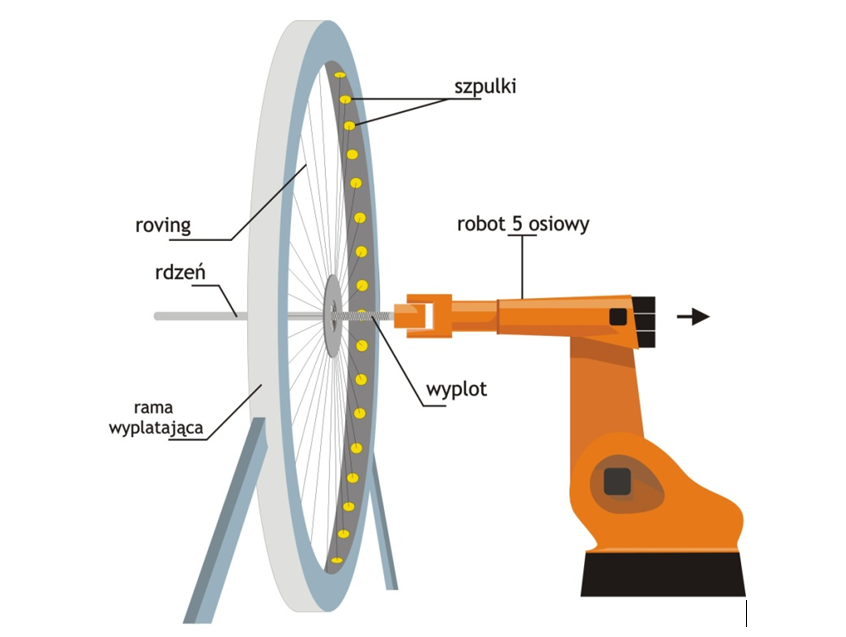
