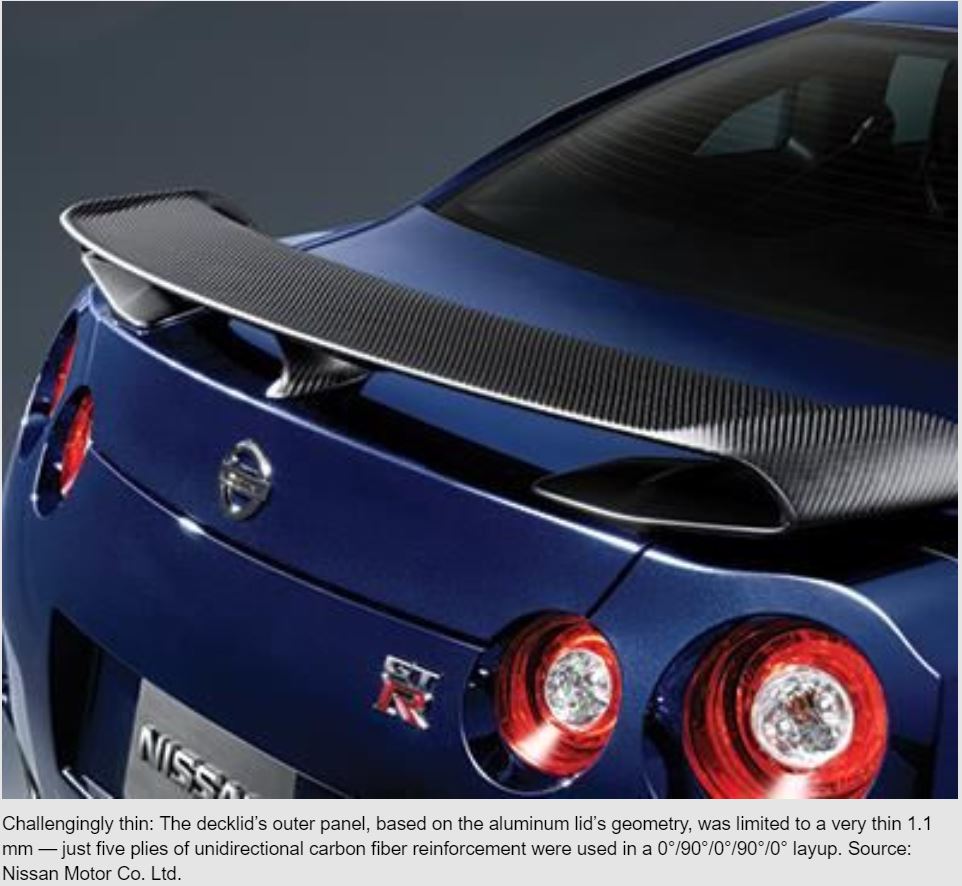
Obecnie, jedną z największych przeszkód wykorzystania materiałów kompozytowych w produkcji elementów do samochodów jest brak opracowanych szybkich procesów produkcyjnych, szczególnie tych bazujących na osnowach chemoutwardzalnych, które potrzebują dłuższego czasu sieciowania. Konwencjonalne prepregi utwardzane w autoklawach pozwalają na otrzymanie elementów o bardzo dobrych właściwościach mechanicznych, ale jest proces ten jest bardzo kapitałochłonny i pracochłonny. Konsumuje również znaczne ilości materiałów eksploatacyjnych, generuje problematyczne odpady, wymaga dużej ilości energii, natomiast cykle produkcyjne mierzone zazwyczaj w godzinach.
Na szczęście w ostatniej dekadzie opracowano technologie pozaautoklawowe (out-of-autoclave OOA), które oferują parametry i jakość wykonanych elementów podobną do autoklawu przy niższych kosztach i znacznie szybszych cyklach produkcyjnych. Bardzo dobrym przykładem jest prepreg compression molding (PCM), które wykorzystuje specjalnie opracowane prepregi z włókna węglowego, które są wstępnie formowane (tzw. preforming), a następnie przenoszone do konwencjonalnej prasy do prasowania na gorąco gdzie następuje formowanie końcowe i utwardzanie.
Jednym z przykładów, które można znaleźć w internecie jest system opracowany przez firmę Mitsubishi Rayon Co. Ltd., który wykorzystano do produkcji elementów karoserii a dokładnie panel wewnętrzny oraz panel zewnętrzny – widoczny pokrywy bagażnika Nissana GT-R, produkowanego przez Nissan Motor Co. Ltd.
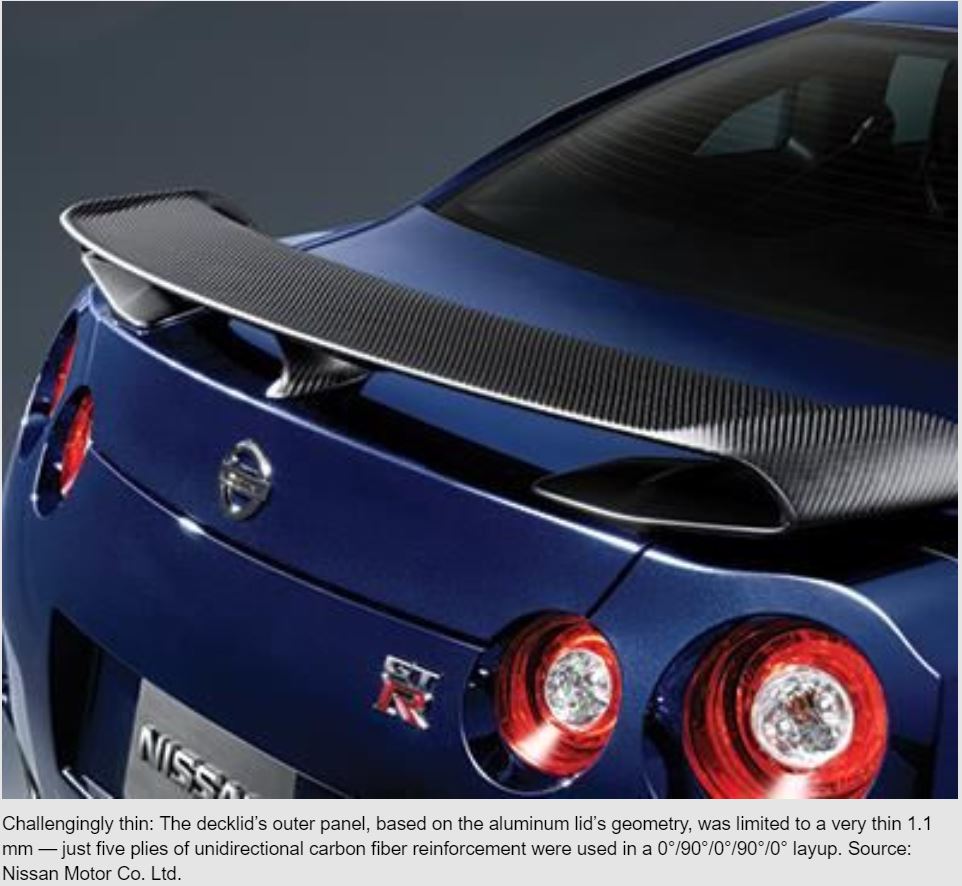
Opracowane prepregi (Pyrofil TR361 E250S) przez firmę Mitsubishi miały specjalnie obniżona lepkość żywicy pozwalającą na ograniczenie wypływania żywicy z formy, a zastosowane utwardzacze pozwalają na przeprowadzenie procesu utwardzania w ciągu 3-5 minut.
Wracając do samego elementu, celem projektu było wykonanie elementu pokrywy bagażnika o takich samych lub lepszych parametrach mechanicznych, ale co najmniej 30% lżejszego w stosunku do pierwowzoru aluminiowego. Dodatkowo konieczne było spełnienie wszystkich wymogów bezpieczeństwa i zapewnienie odpowiedniego zachowania się pokrywy podczas prób zderzeniowych, które odrzucało możliwość destrukcji elementu do postaci małych fragmentów.
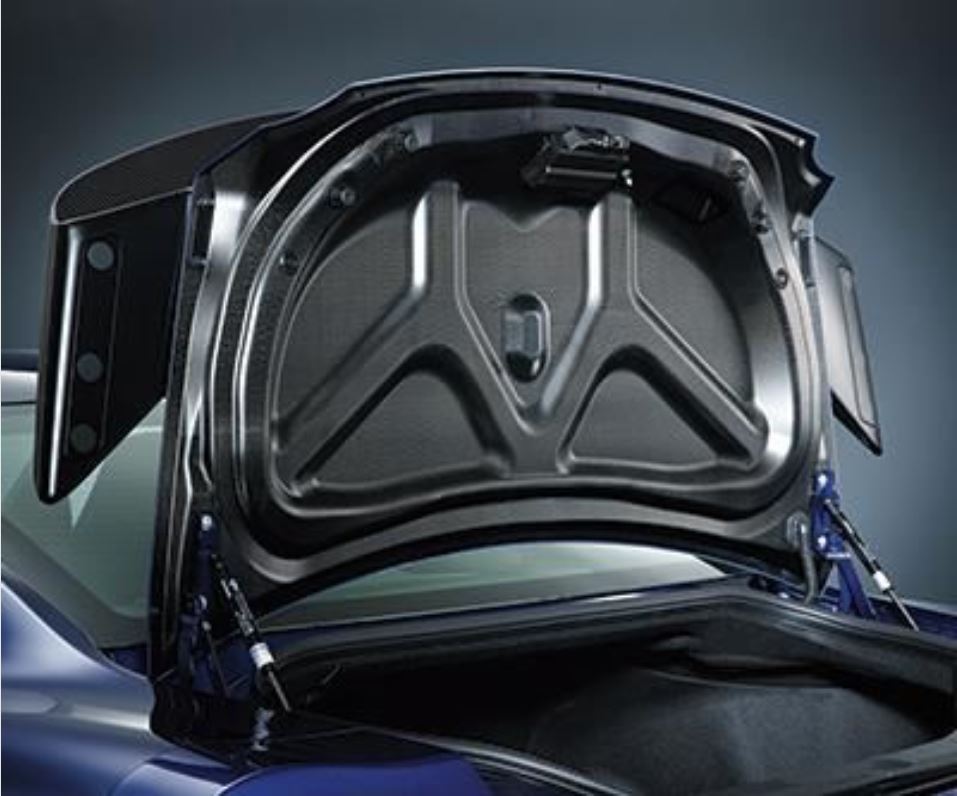
Ważna była również prędkość formowania, ze względu na obniżenie kosztów produkcji i możliwość zastosowania rozwiązania w niższych modelach Nissana. Oczywiście na końcu liczy się jakość i cena.
Sam proces wyglądał następująco. W produkcji prepreg jest najpierw przycinany i układany warstwowo w formie wykonanej z płyty modelarskiej z poliuretanu . W narzędziu tym prepreg jest formowany poprzez podgrzewanie przez 1 minutę, aż do osiągnięcia temperatury 60-70°C i natychmiast formowany wstępnie w prasie pneumatycznej pod ciśnieniem (0,3 MPa). Preformy są następnie schładzane do temperatury pokojowej. W kolejny kroku preformy są ostatecznie formowane w prasie hydraulicznej w czasie 8 minut i temperaturze 140°C, przy użyciu ciśnienia formującego 8 MPa.
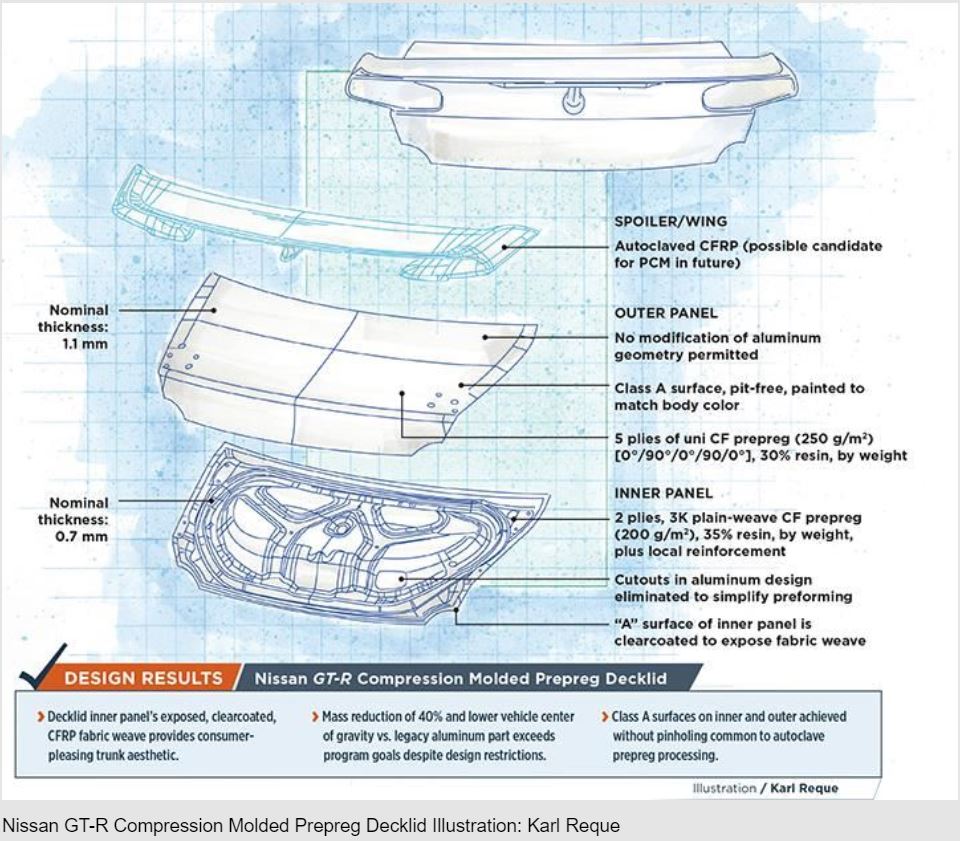
Głównymi zaletami tego rozwiązania była znaczna redukcja masy gotowego elementu, aż o 40%, co pozytywnie wpłynęło na jakość obsługi samej pokrywy bagażnika, łatwiejsze i szybsze otwieranie, a w konsekwencji również na obniżenie zużycia paliwa.
Jak przedstawili producenci wykorzystanie technologii prepreg compresion moulding pozwala na wykonanie na jednym narzędziu 50000 szt. rocznie elementów pokrywy bagażnika stosując utwardzacz 5 minutowy, ale już przy wykorzystaniu utwardzacza 3 minutowego wydajność wzrasta do 80000 szt. rocznie. Wykorzystanie typowych pras hydraulicznych których ciśnienie formowania jest na poziomie 8 MPa pozwala również na rozpoczęcie produkcji ze starszym parkiem maszynowym.